INDUSTRY-LEADING DURABILITY
Siding that stands up to the elements
Hardie® fiber cement products resist damage from fire, water, weather, pests, and time—helping protect your most precious asset for the long haul.
Help shield your home from unexpected damage
Fire resistance
Hardie® fiber cement siding will not ignite when exposed to a direct flame —nor contribute fuel to a fire.* In contrast, fire feasts on wood and melts vinyl almost instantly.
Moisture resistance
Hardie® products are engineered to resist water and humidity—and will stand up to rain, sleet, and snow better than wood-based siding, which will swell and expand more when exposed to moisture.
Weather resistance
Hardie® products are made to withstand worst-case weather: hurricanes, rain storms, strong winds, extreme heat, UV rays, humidity, snow, hail, freezing temperatures, and more.
Pest defense
Hardie® siding holds no appeal for pests and won’t be eaten by termites, while engineered wood and natural wood siding are vulnerable to woodpeckers and other pests.
Color that looks better—and lasts longer—than paint
With our proprietary ColorPlus® Technology finishes, you get more than gorgeous color—you get years of lasting character and fade resistance. Our factory-applied, baked-on color is cured between coats, creating a strong bond that resists peeling, chipping, and cracking for years to come.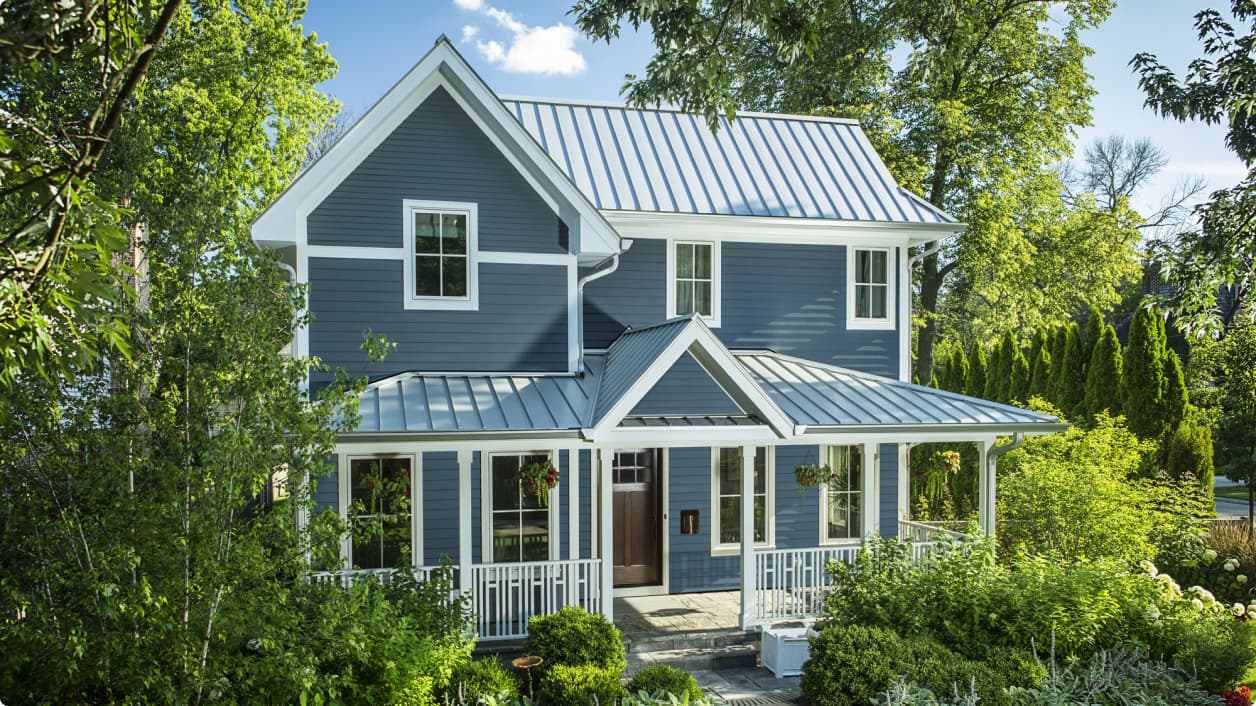
Mother nature meets her match
Only Hardie® products are Engineered for Climate® to ensure you get unmatched protection and performance—no matter where you live. Built to defy even the most extreme weather in your specific area, Hardie® siding stands up to blistering sun, hurricane-force winds, brutal humidity, extreme cold, sheets of snow, and more.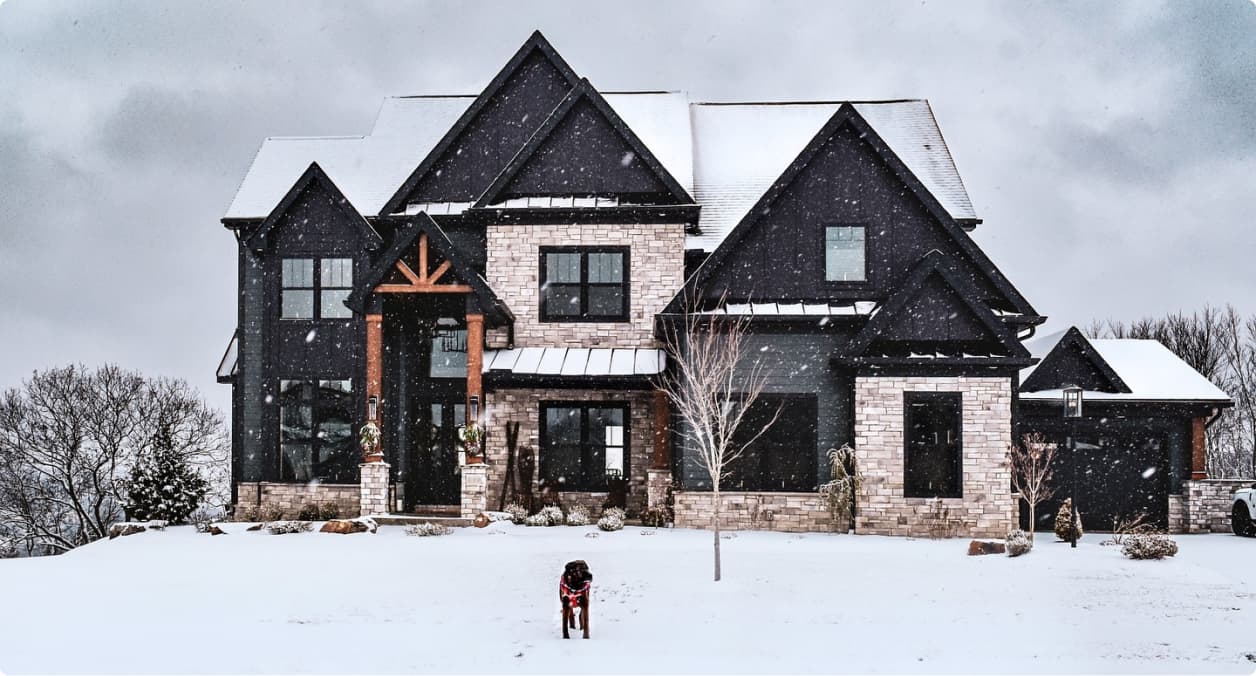
Why choose James Hardie?
As the trusted industry leader, James Hardie provides distinct style, high performance, next-level innovation, and a lifetime of value.
Put our products to the test
Explore our catalog to discover why homeowners and pros alike choose Hardie® products.