Building a Culture of Sustainability
Sustainability is foundational at James Hardie. We know that from our front-line employees to the builders who use our products, each person plays a role in our success.
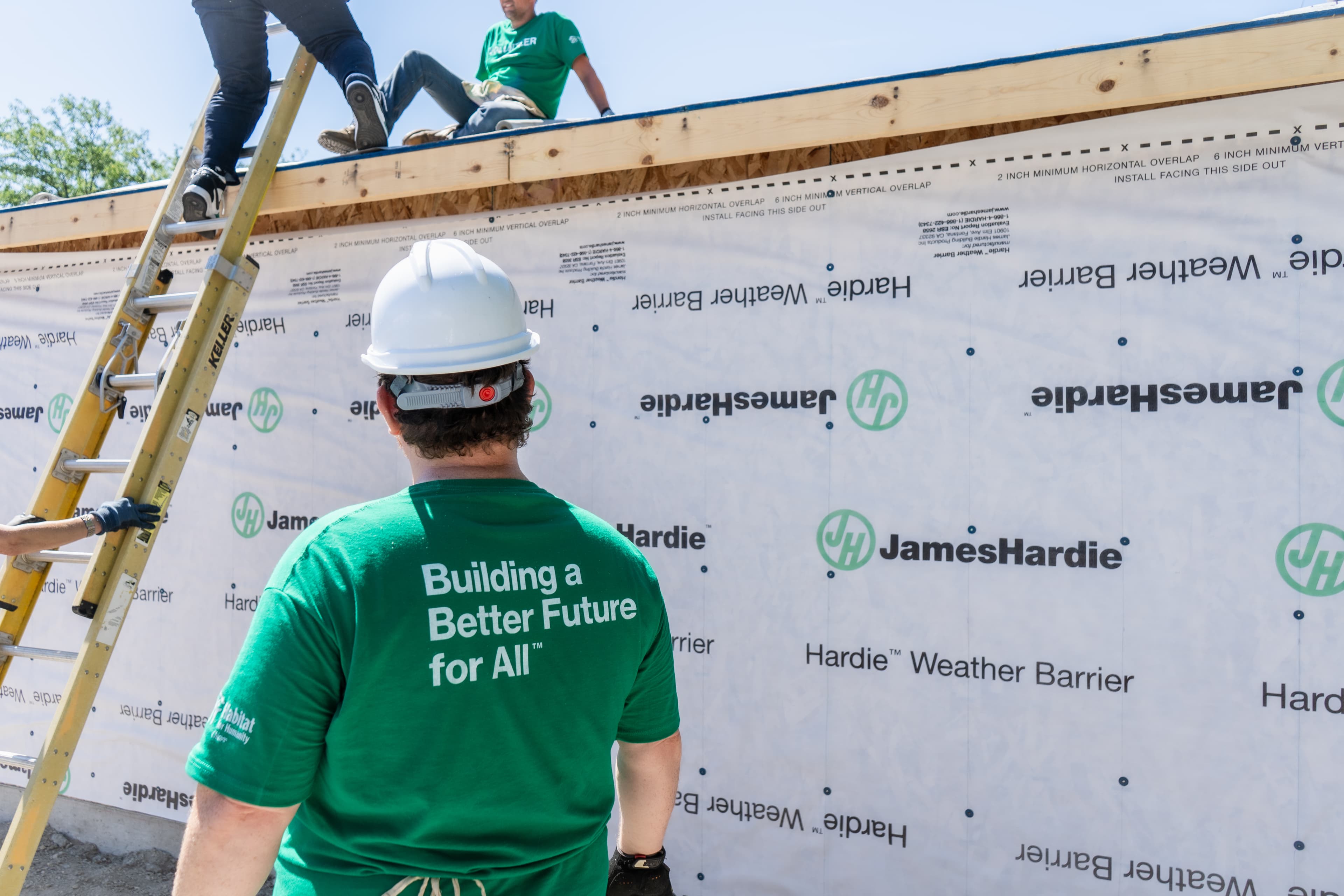
Sustainability is a never-ending journey for James Hardie. Last year, we set new ambitious goals to reduce Scope 1 + 2 emissions, recycle water, minimize waste, increase diversity and prioritize safety. Our new sustainability report details our progress toward achieving our targets.
Clear goals, measurable outcomes, and transparency are key components of an effective sustainability strategy. But just as important to the ultimate success is ensuring these goals are foundational in a company’s business operations, governance structure, and company culture. I would argue that building a culture of sustainability is a critical element of a successful sustainability strategy.
I am proud that sustainability is foundational at James Hardie. As we focus on each element of our value chain, we know that from our front-line employees to the builders who use our products, each person plays a role in our success. These examples from our annual sustainability report tell the story of our progress and inspire us to keep building on our success.
Integrating processes
We continue to integrate sustainability into our Hardie™ Manufacturing Operating System (HMOS) at all levels of our operations. Ryan Kilcullen, executive vice president of global operations with James Hardie, reinforced this commitment by saying, “Ensuring that our sustainability efforts are part of HMOS reinforces to our workforce that this is how we intend to operate our plants and deliver against our targets moving forward. HMOS encompasses our culture of continuous improvement and LEAN manufacturing and empowers our people to champion improvements to environmental performance.”
In one example, finishing operator, Jeff Riley, has done an outstanding job of supporting a more efficient wastewater treatment system. This system removes solids from paint wash to allow water to be recycled back into our manufacturing process. We have reduced liquid waste paint collections by 93 percent from peak, eliminating 130 metric tons of liquid waste disposal per month and delivering significant cost savings of over $40,000 a month at this site.
Teaming up to tackle waste
Finding beneficial uses for the materials left over from our operations is a key driver toward achieving our goal of zero manufacturing waste to landfill by 2035. We collaborate with companies throughout our supply chain to keep waste materials in the value stream.
At six plants in North America, we are collaborating with our suppliers to pilot recycling solutions that have been successfully used by our Asia-Pacific operations for over 15 years. Rejects that don’t meet our high-quality standards are crushed by local cement providers and used to supplement raw materials in new cement production.
Raising the bar on water
Water is a scarce and valuable natural resource. We are raising the bar and setting new internal standards, going beyond regulatory requirements, by pursuing water recycling opportunities as appropriate by site. Engineers Kristen Dornstauder and Jody Lambert are key members of a team investigating water use in our plants. They contributed to a project to install an air conditioner condenser in the autoclave system at our Summerville, South Carolina plant to redirect 12,000 to 18,000 gallons of discharge water a day to be reused.
Creating a healthier work environment
Safety is embedded in our global corporate culture through our Zero Harm standards and our commitment to continuous improvement. James Hardie made a significant global investment in safety infrastructure projects last fiscal year, including upgrading equipment used when working from heights, installing more than 1,200 machine guards to provide additional protection for employees and promoting risk awareness.
In FY24, we reduced our DART (Days Away, Restricted or Transferred) rates globally. In Rosehill, Australia, plant manager Hector Castro and his procurement team spearheaded an innovative effort to incorporate three new electric forklifts into manufacturing and distribution. These efforts eliminated worker exposure to forklift emissions, contributing to a healthier work environment.
Promoting a positive, inclusive workplace
We strive to make James Hardie a place where employees want to work, as well as build their careers. Our Employee Resource Groups (ERGs) promote a positive and inclusive work environment through local, specialized programs. As a leader in the AMIGOS ERG, claims coordinator Nancy Phan helps implement meaningful improvements for our Hispanic and Latino colleagues. For example, AMIGOS recently lead an effort to expand the amount of benefit information in available Spanish.
Creating positive impact
Striving to positively impact people and families in the areas where we operate and where our products are used is part of the James Hardie culture. From our employees to our senior leaders, everyone is empowered to drive change in their communities. We have proudly supported Habitat for Humanity® International for many years. Our sites have donated product, and hundreds of our employees have given their time and talents to build Habitat homes. We are stepping up our engagement as a corporate sponsor of the Habitat Strong program, which addresses the need to build affordable and climate-resilient homes that can withstand severe weather conditions and natural disasters.
Beautiful products, exceptional durability and resilience
James Hardie is firm in its commitment to develop beautiful products with exceptional durability and resilience to extreme weather. We collaborate with builders and remodelers to develop solutions suited to the demands of a changing climate. We’re proud that our products were selected by three leading home builders from across the U.S. in FY24. Learn more here.
As each of these examples illustrate, our progress has been possible through collaboration and innovation across the value chain. We’re proud of the work we’ve done, and we know we have more to do. Together, we aim to put sustainability into action, doing right by our planet, our people and the communities we serve.